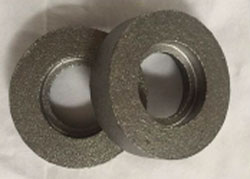
ارزیابی ضریب اصطکاک در شکل دهی گرم
متغیرهای متعددی بر فرایند شکل دهی فلزات تأثیر گذار میباشند که یکی از مهمترین آنها اصطکاک است. اصطکاک تاثیر زیادی بر تغییر شکل ماده ، نیروی لازم برای شکل دهی ، کیفیت سطحی محصول و سایش دارد. برای تعیین میزان و نحوهی تأثیر آن داشتن مقدار دقیق ضریب اصطکاک ضروری است. از این گذشته اصطکاک به عنوان یکی از پارامتر های ورودی برای مدل سازی و تحلیل فرآیند های شکل دهی مورد احتیاج است . بنابراین مطالعه ی شرایط اصطکاکی در فصل مشترک قالب – قطعه به عنوان یکی از متغیر های اصلی فرآیند های شکل دهی می بایست مورد توجه قرار گیرد. تغییرات اندازه قطر داخلی حلقه در حین تغییر شکل به میزان ضریب اصطکاک برشی وابسته است. بنابراین بررسی تغییرات قطر داخلی نمونه راهکاری مناسب برای ارزیابی شرایط اصطکاکی خواهد بود. آزمون فشار حلقه با روانکاری مختلف انجام شده است. منحنی های کالیبراسیون به کمک شبیه سازی المان محدود رسم شد و فاکتور اصطکاک برشی برای هر یک از روانکارها بدست آمده است. نتایج بهترین حالت روانکاری برای کار گرم در هر کدام از آلیاژها را نشان می دهد.
به طور کلی در فرآیند های شکل دهی همواره به دنبال تولید محصولی سالم و بدون عیب با کمترین میزان استفاده و ویژگی های فصل مشترک تماسی از قبیل اصطکاک لازم است . در این میان اصطکاک یکی از مهم ترین پارامتر هایی است که تأثیر بسیار زیادی بر تغییر شکل ماده ، نیروی لازم برای شکل دهی ، کیفیت سطحی محصول و سایش قالب خواهد داشت. از این گذشته اصطکاک به عنوان یکی از پارامتر های ورودی برای مدل سازی و تحلیل فرآیند های شکل دهی مورد احتیاج است . بنابراین اصطکاک نقش اساسی در کل فرآیند شکل دهی دارد و می بایست در حین طراحی فرآیند نقش آن در نظر گرفته شود . الگوی جریان مواد و عیوب ایجاد شده در قطعات تولیدی تحت تأثیر شرایط اصطکاکی کنترل می شود . انتخاب روش آزمایش مناسب با توجه به نوع فرآیند شکل دهی برای تعیین صحیح فاکتور ( و یا ضریب ) اصطکاک و درک پدیده اصطکاک در سطح تماس قالب و قطعه تحت شرایط روانکاری مختلف مهم است.
امروزه شکل دهی فلزات به عنوان یکی از روش های مهم ساخت و تولید قطعات محسوب می شود . به همین دلیل شناخت هر چه دقیق تر خواص مواد ، پارامتر های فرآیند های شکل دهی ، ابزار شکل دهنده و رفتار بین قالب و قطعه ( همانند اصطکاک ) باعث تولید محصول نهایی بدون عیب و کمترین مصرف مواد و هزینه ی ابزار می شود[۱].
تاکنون روش های مختلفی برای بررسی اصطکاک در فصل مشترک قالب و قطعه پیشنهاد گردیده است ، که در میان آن ها می توان به آزمون فشار حلقه ، آزمون اکستروژن دو فنجانی ، آزمون لبه دار کردن ، آزمون فشار T – شکل و . . . اشاره کرد . به کمک این آزمایش ها می توان به ارزیابی کارآیی روانکار های مختلف مورد استفاده در فرآیند های شکل دهی پرداخت و در هر حالت شرایط اصطکاکی را به صورت کمی ( در قالب فاکتور و یا ضریب اصطکاک ) تخمین زد.
لازم به ذکر است در تعیین فاکتور ( و یا ضریب ) اصطکاک به وسیله ی روش های فوق برای فرآیند های شکل دهی گرم ، علاوه بر اثرات روانکاری ، اثرات خنک شدن قالب یا انتقال حرارت از ماده داغ به قالب و ابزار سرد تر هم باید در نظر گرفته شود . چرا که قابلیت و کارکرد روانکار در دماهای مختلف متفاوت خواهد بود. از این رو آزمایش های روانکاری مورد استفاده برای تعیین اصطکاک باید هم شامل اثرات روانکاوی و هم اثرات خنک شدن قالب باشند . بنابراین مطالعه ی شرایط اصطکاکی در شکل دهی گرم یک آزمایش مناسب می باید در نظر گرفته شود [2].
– دمای نمونه و قالب باید تقریبا مشابه با دماهایی باشد که در فرآیند شکل دهی گرم وجود دارد .
– مدت زمان تماس بین نمونه و ابزار تحت فشار باید تقریبا مشابه با عملیات شکل دهی مورد نظر باشد.
– مقدار انبساط سطحی نمونه ( نسبت مساحت سطح تغییر شکل یافته به مساحت سطح اولیه نمونه ) باید تقریبا مشابه مقدار آن در فرآیند مورد مطالعه باشد .
– سرعت نسبی بین قطعه و قالب ها باید تقریبا همان مقدار و جهتی را داشته باشد که در فرایند شکل دهی مورد مطالعه وجود دارد .
– ابزار آزمایش ( همانند کوبه دستگاه پرس ) از ماده ای ساخته شده باشد که در فرآیند شکل دهی استفاده می شود.
در میان آزمون های مختلفی که برای تخمین کمی اصطکاک بین قالب و قطعه در فرآیند های شکل دهی فلزات پیشنهاد شده است ، آزمون فشار حلقه یکی از مهم ترین و پرکاربرد ترین آزمون ها محسوب می گردد . آزمون فشار حلقه یکی از روش های ارائه شده به منظور محاسبه ی فاکتور و یا ضریب اصطکاک بین قطعه و قالب در فرآیند های شکل دهی سرد و گرم می باشد . این آزمون نخستین بار در مطالعات انجام گرفته توسط کونوگی،کودو و جانسون ارائه گردید و بعد ها توسط محققین دیگر همچون میل و کوککرافت توسعه یافت[۱].
در آزمایش فشار حلقه قطر داخلی حلقه در طی تغییر شکل تغییر میکند. به طور کلی میتوان گفت که اگر قطر داخلی نمونه در طی تغییر شکل افزایش یابد، اصطکاک کم است و اگر قطر داخلی نمونه در طی تغییر شکل کاهش یابد، اصطکاک زیاد است. با استفاده از این ارتباط، منحنیهایی که ارتباط بین درصد کاهش قطر داخلی نمونهها با کاهش ارتفاعشان را برای مقادیر مختلف اصطکاک نشان میدهند، ایجاد شدند.
بعد از این که میل و کوکوکرافت مقاله خودشان را در زمینه ضریب اصطکاک منتشر کردند، تحقیقات زیادی توسط دیگر محققان در این زمینه انجام شد. میل در سال ۱۹۶۵ نشان داد که ضریب اصطکاک با تغییرات دما تغییر میکند. هرچه دما بالا میرود مشاهده میشود که ممکن است ضریب اصطکاک به سمت اصطکاک چسبنده پیش برود یا ممکن است وابسته به جنس مواد حلقه کاهش یابد. وی هم چنین در سال ۱۹۶۶ تحقیقی برای یافتن اختلاف در ضریب اصطکاک فلزات در طی تغییر شکل فشاری در دمای اتاق انجام داد. نتایج او نشان داد که ضریب اصطکاک با افزایش نرخ تغییر شکل برای مواد مختلف تمایل به زیاد شدن دارد [3].
رابینسون [۱] به مطالعه آزمایش فشار حلقه به کمک آزمایشات تجربی و شبیه سازی المان محدود پرداخت و منحنیهای کالیبراسیون را با شرایط روانکاری مختلف برای پلاستیسین ارایه داد. فلدر آزمایش فشار حلقه را در دمای ۱۲۵۰ درجه سانتی گراد بر روی استیل انجام داد. نتایج نشان داد که سرعت ابزار شکل دهی اثر مهمی روی اصطکاک دارد و نشان دادند که اصطکاک با افزایش سرعت، کاهش مییابد.
حسن سوفوقلو [4] منحنیهای کالیبراسیون اصطکاکی را با کمک شبیه سازی المان محدود و مدل سازی فیزیکی به دست آوردند و نشان دادند که پارامترهای مواد و شرایط آزمایش اثرات مهمی روی شکل منحنیهای کالیبراسیون اصطکاکی برای هر دو حالت شبیه سازی و مدل سازی فیزیکی دارد. میل مطالعهای به منظور مشاهده این که کدام یک از حالتهای اصطکاک تعریف واقعیتری از شرایط اصطکاک در فرایند شکل دهی دارد، انجام داد و نشان داد که m به عنوان شاخص عددی برای تعریف شرایط اصطکاکی در عملیات کله زنی نسبت به ضریب اصطکاک واقعیتر است. همچنین مشخص شد که آزمایش فشار حلقه تکنیک دقیقی برای تعیین منحنی تنش-کرنش واقعی در عملیات شکل دهی است.
شهریاری به تعیین ضریب اصطکاک برشی در شکل دهی داغ سوپر آلیاژ نایمونیک ۱۱۵ تحت روانکارهای مختلف با استفاده از مشاهدات فیزیکی و شبیه سازی المان محدد پرداختند. یانچون ژو به تعیین ضریب اصطکاک برشی برای آلیاژ تیتانیوم Ti – 6A1 – 4 V در فرایند شکل دهی داغ به وسیله آزمایش فشار حلقه به صورت آزمایش فیزیکی و شبیه سازی المان محدود پرداخت.
مدلهای اصطکاکی
روشهای تئوری متعددی برای تعیین منحنیهای کالیبراسیون برای آزمایش فشار حلقه وجود دارد. این روشها بر اساس آنالیز تختال، روش کرانه بالا و روش آنالیز المان محدود هستند.
لازم به ذکر است که مدلهای تئوری مختلفی برای بررسی اصطکاک وجود دارد که در ادامه به سه مدل به صورت مختصر اشاره میشود.
1- مدل اصطکاکی کولمب
مدل اصطکاکی کولمب بر پایه قانون آمونتون یکی از مدلهای اصطکاکی است که معمولاًً در برنامههای کامپیوتری المان محدود استفاده میشود. به صورت رابطه (2-1) بیان میشود.
(2-1) τ= μ .p
که τ تنش برشی اصطکاکی، μ ضریب اصطکاک در سطح مشترک قطعه و قالب و p نیروی عمودی وارده میباشد. این قانون برای حالت الاستیک و نیز برای فرایندهای شکل دهی با فشار کم معتبر است [3].
2- مدل اصطکاکی برشی
این مدل برای حالتهایی که فشار زیادی در سطح مشترک قطعه و قالب وجود دارد استفاده میشود. به صورت رابطه (2-2) بیان میشود [3].
(2-2) τ=m .k
که m ضریب اصطکاک برشی است که از مقادیر m = 0 برای سطح بدون اصطکاک تا m = 1 برای اصطکاک چسبنده را شامل میشود. و k حد تسلیم برشی است.
بنا به کار آویتزور [3] میانگین ضریب اصطکاک کولمب، μ، میتواند با استفاده از معادله زیر برای اندازه گیری m استفاده شود:
(2-3) k=σ_0/√3
(2-4) μ=m/√3 (σ_0/P_ave )
که σ_0 حد تسلیم و P_ave میانگین فشار در سطح است.
3- مدل اصطکاکی عمومی
این مدل ترکیبی از دو مدل ذکر شده در بالاست که با معادله (2-5) بیان میشود.
(2-5) τ=f ∝k
ضریب اصطکاک μ یا فاکتور برشی اصطکاک (m , k) به عنوان اعداد بدون بعد برای هم سانی در شرایط اصطکاک در نظر گرفته میشود. با استفاده از روشهای تحلیلی۷ مجموعههای مختلفی از منحنیهای کالیبراسیون برای تعیین m یا f برای یک روانکار مخصوص به دست میآید. شکل این منحنیها تحت تأثیر هندسه اولیه حلقه استفاده شده در آنالیز میباشد. در این تحقیق، کله زنی داغ آلیاژ آلومینیوم ۶۰۸۲ با فشار زیاد در سطح مشترک انجام میشود. بنابراین مدل اصطکاکی ثابت به عنوان مدل اصطکاکی در سطح تماس در نظر گرفته میشود[3].
برای اندازه گیری ضریب اصطکاک در فرآیند های شکل دهی فلزات از آزمون های شبیه ساز استفاده می شود.از جمله این آزمون ها آزمون فشار حلقه است.در این آزمون مطابق آنچه که گفته شد یک حلقه توسط فک های دستگاه پرس تحت فشار قرار گرفته و ارتفاع آن کاهش می یابد.با توجه به میزان اصطکاک بین سطح حلقه و فک پرس، حلقه در طی تغییر شکل بشکه ای می شود. و ضریب اصطکاک با توجه به ابعاد حلقه میزان کاهش قطر داخلی و درصد کاهش ارتفاع از روی نمودارهای تجربی بدست می آید.