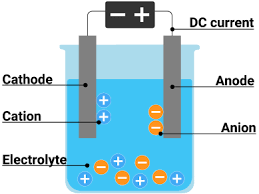
آبکاری و آماده سازی سطح(بخش 1)
آبکاری وآماده سازی سطح
تکنولوژی آبکاری بیش از 2000 سال است که وجود دارد ودر طول دوهزاره گذشته به طور پیوسته مورد استفاده قرار گرفته است. تکنولوژی آبکاری مدرن علاوه بر کاربرد صنعتی برای تمامکاری سطحی، برای فرایندهای جدید به منظور ساخت فیلم هایی با کارآیی زیاد یا بدنه هایی با ریز ساختار ریز در صنایع میکروالکترونیک مورد استفاده قرار گرفته است.
پوشاندن یک جسم با یک لایه نازک از یک فلز با کمک یک سلول الکترولیتی آبکاری نامیده می شود. جسمی که روکش فلزی روی آن ایجاد می شود رسانای جریان برق است. الکترولیت مورد نظر برای آبکاری باید حاوی یون های آن فلزی باشد که قرار است لایه نازکی از آن روی جسم قرار بگیرد. فرآیندی که آبکاری به وسیله آن انجام می شود، رسوب دهی الکتریکی نام دارد.کاتد قطعه ای است که قرار است لایه روی آن بنشیند و آند فلزی است که روکش است. این دو به وسیله الکترولیت با هم در ارتباط الکتریکی دارند و با بکاربردن یکسو کننده جریان مستقیم به آند می رسد و باعث انحلال اتمهای آن می شود. در سوی دیگر، این اتم ها با احیا در فصل مشترک کاتد و الکترولیت، بر روی آن رسوب می کنند.
فرآیند آبکاری الکتریکی اساساً برای رسوب دادن نیکل، طلا یا نقره جهت افزایش ارزش فلزات پایه مانند آهن، مس وغیره و همچنین ایجاد روکشی بسیار مناسب (در حد میکرومتر) برای استفاده از خواص فلزات روکش کاربرد دارد. اکثر فرآیندهای آبکاری الکتریکی صنعتی در محلول های آبی انجام می شوند. با این وجود، انواع فلزاتی را که می توان با استفاده از الکترولیت های آبی رسوب نشانی کرد محدود هستند.
امروزه آبکاری الکتریکی تا حدی توسعه یافته است که نه تنها مرحله نهایی تولید بعضی محصولات است بلکه برای ایجاد پوششهای محافظی مثل کادمیم، کروم یا اکسید آلومینیوم روی قطعات به کار می رود. اساس آبکاری الکتریکی به این صورت است که در اثر عبور جریان مستقیم از یک الکترولیت فلز محلول در آن روی کاتد رسوب کرده و متعاقباً مقداری از فلز آند وارد محلول می شود به این ترتیب الکترولیت ثابت می ماند. آبکاری الکتریکی برای ایجاد پوشش های تزئینی و محافظ، اصلاح سطوح ساییده شده یا اضافه ماشینکاری شده، قطعه سازی یا به عبارتی شکل دهی الکتریکی قطعات شکل پیچیده که دارای زوایای مقعر، ابعاد دقیق و سطوح طرح دار هستند، عملیات آندکاری، تمیزکاری الکترولیتی، پرداخت الکترولیتی، اسید شویی آندی، استخراج و تصفیه فلزات به کار می رود.
متغیرهای ممکن پیش از آبکاری عبارتند از:
ماده زیر لایه(فلز،غیرفلز)-پیش عملیات مواد زیر لایه(اکسیدزدایی، گریس زدایی، شستن، خشک کردن)- نوع فلزات(فلز خالص، آلیاژ)-غلظت محلول(غلظت، ترکیب آلیاژ)-نوع نمک های فلزی(اثر نوع آنیون)- نوع و مقدار عوامل کمپلکس-PH محلول، PH تنظیم کننده، PH بافر-افزودنی ها (براق کننده، عامل یکنواخت کننده، کاهنده تنش، الکترولیت کمکی)-چگالی جریان(جریان مستقیم، پالسی، چگالی جریان آندی/کاتدی)-ولتاژ اضافی-شکل تانک آبکاری-نوع مواد آند(قابل حل، غیر قابل حل)-فاصله بین الکترودی-تلاطم(ایستا، همزن، حباب زا، فراصوتی، ارتعاشی)-دمای آبکاری و شرایط دیگر
شرایط متغیر در طول آبکاری الکتروشیمیایی عبارتند از:
غلظت فلز-مصرف افزودنی ها-PH-تغییر ساختاری عامل کمپلکس کننده- دمای محلول-از رسوب نشانی روی مواد زیر لایه تا رسوب نشانی روی فیلم آبکاری شده- تغییر مورفولوژی سطحی با افزایش ضخامت فیلم- تغییر پتانسیل به دلیل شرایط جریان ثابت-تغییر چگالی جریان به دلیل پتانسیل ثابت- تولید گاز هیدروژن روی کاتد- تصاعد گاز آند و شرایط دیگر
ضخامت پوششهای رسوب ـ الکتریکی به دانسیته جریان، راندمان جریان و مدت زمان عملیات بستگی دارد. خواص فیزیکی تابع دانسیته جریان، دما ، ترکیب حمام، کیفیت سطحی قطعه و عوامل افزودنی به حمام است. از این نظر نمکهای آبکاری الکتریکی اهمیت زیادی پیدا کرده اند به طوری که روز به روز تقاضای آنها افزایش می یابد.
کیفیت رسوب الکتریکی بر حسب کاربرد آن متفاوت است اگر هدف از آبکاری جلوگیری از زنگ زدن فولاد باشد ممکن است پوشش نازکی هم کافی باشد ولی اگر شفافیت رسوب نیز مهم باشد در این صورت کیفیت بالاتری طلب خواهد شد. کیفیت رسوبهای نازک از طریق آزمایش اندازه گیری ضخامت و مقاومت خوردگی تعیین می گردد. روشهای زیادی برای جلوگیری از خوردگی وجود دارد که یکی از آن ها ایجاد روکشی مناسب برای فلز ها می باشد. رنگین کردن فلزات-لعابکاری-آبکاری با روکش پلاستیک- حفاظت کاتدیک و آبکاری با فلزات دیگر از معمول ترین روشهای روکش فلزها می باشد.
در آبکاری الکتریکی شستشو دادن، آبکشی ، اسیدشویی و چربی گیری اهمیت زیادی دارد.
1- شستشو : این کار توسط انواع تمیز کننده های قلیایی انجام می گیرد انتخاب نوع آن به موادی که باید شسته شوند و همین طور روش شستشو (غوطه وری خالص یا با استفاده از سیستم الکتریکی) بستگی دارد.
۲- چربی گیری : قبل از شستشوی الکتریکی چربی گیری انجام می گیرد. به این صورت قطعات را در حلالهای سرد غوطه ور کرده یا در معرض بخار داغ قرار می دهند. بخار حلال روی فلز کندانس شده و چربی را حل می کند.
۳- اسید شویی : در فرآیند های آبکاری برای تأمین سطح فعال باید فیلمهای غیرآلی سطح شامل پوسته های اکسیدی یا محصولات زنگ از سطح حذف شوند. در غیر این صورت چسبندگی رسوب به سطح کار ضعیف شده و ممکن است رسوب حفره ـ حفره و یا پوسته ـ پوسته گردد.
۴- آبکشی : آبکشی ممکن است به صورت غوطه وری در آب جاری یا با استفاده از اسپری انجام شود. بعضی وقتها برای اطمینان از خارج شدن نمکهای سطحی ممکن است آبکشی تکرار شود.
برای پاک کردن مواد روغنی با گریس روی سطح قطعات آنها را در محلول قلیایی و سپس در آب گرم غوطه ور می کنند. برای جلوگیری از خوردگی یا زنگ زدن ممکن است آبکشی در آب سرد نیز انجام بگیرد.
زنگ آهن، زنگ مس از طریق شستشو در اسیدهای معدنی رقیق حذف می شوند. برس کاری به راحت کنده شدن پوسته های سطح کمک می کند. در صورتی که بعد از اسیدشویی ابتدایی پوسته ها کاملاً پاک نشوند می توان عملیات را تکرار کرد.
تمیزکاری الکترولیکی، فرآیند حذف کردن پوسته های سطحی در محلول با استفاده از جریان الکتریسیته است. تمیزکاری مکانیکی، تمیزکاری مکانیکی مکمل تمیزکاری شیمیایی و الکتروشیمیایی است.
در این روش ابتدا به منظور پاک کردن چربیهای سطحی قطعات را توسط محلول پتاس شستشو داده و سپس در محلول اسیدی غوطه ور می کنند. بعد از مدت زمان مناسبی قطعات را خارج کرده و آبکشی می نمایند. در این حالت با استفاده از برس سیمی (به صورت دستی یا سنگ دستی) می توان مواد زاید سطحی را براحتی حذف کرد.